InfraRed Thermometry System Control
InfraRed Thermometry (IRT) is the first self-adjusting control system for RotoSpeed rotational molding machines. By continuously monitoring the surface temperature of the mold, IRT senses anomalies in the molding cycles that can cause scrap parts and automatically adjust oven or cool times to ensure optimum results — removing your dependence on the operator and creating a machine that is adaptive to ambient conditions.
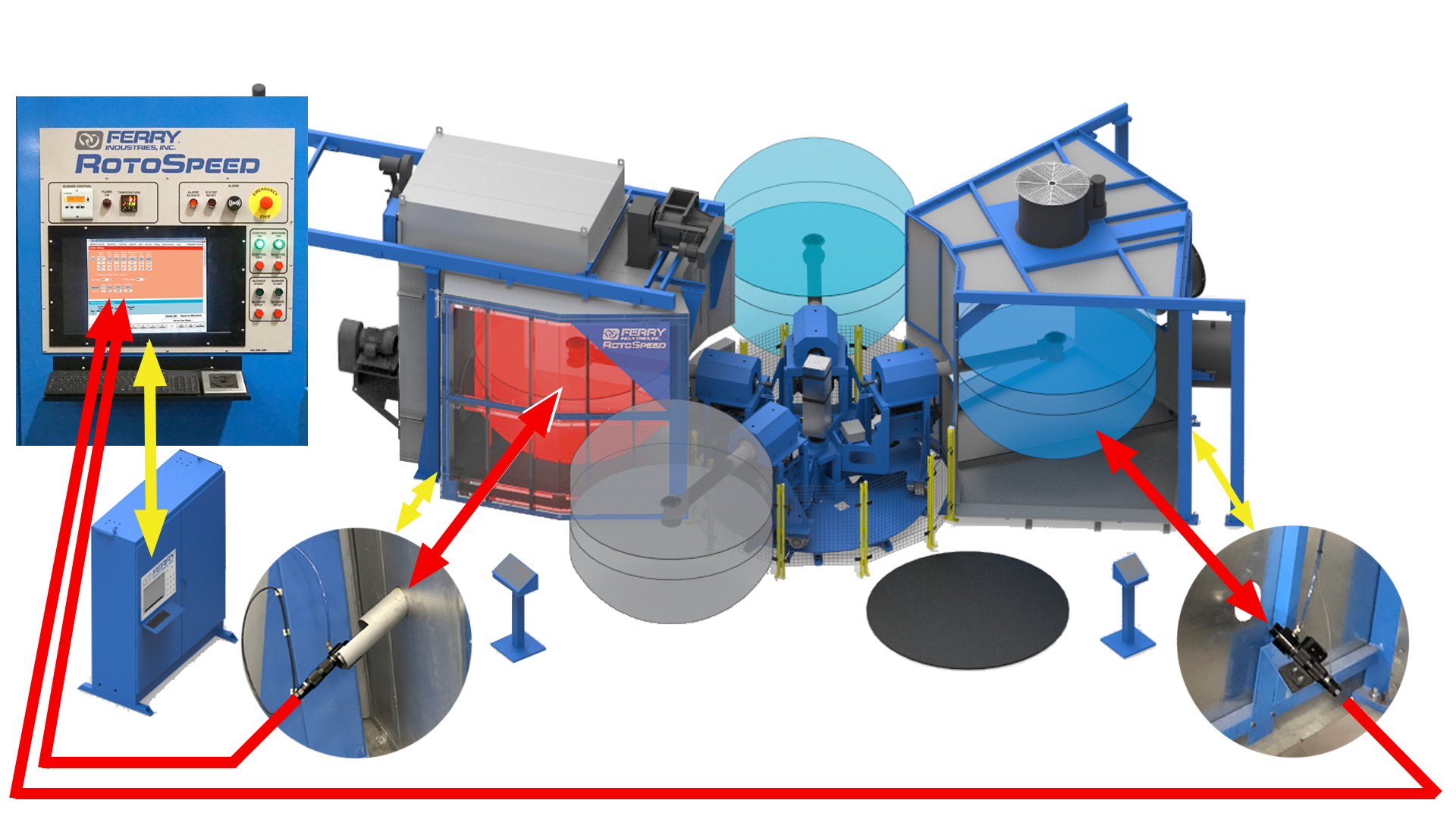
IRT uses remote sensors at the Oven and Cooler stations to monitor the temperature of the surface of the rotating molds and interprets this data for analysis. This map of temperature is used to provide key data values during the heating and cooling cycles; then this data is used to determine the end of the oven and the cooling cycles for repeatable cycles.
Features of IRT include:
Ability to integrate into Ferry RotoCure System Manager
Improves part consistency
Cycles are adaptive to ambient temperature changes — decreases scrap
Recovers from operator- or machine- induced faults
No thermocouple wires to connect
Saves valuable machine time–no need to pre-heat the oven
Provides for optimum cure and part properties
Saves time by preventing cycle redundancy
Assists dimensional stability of parts
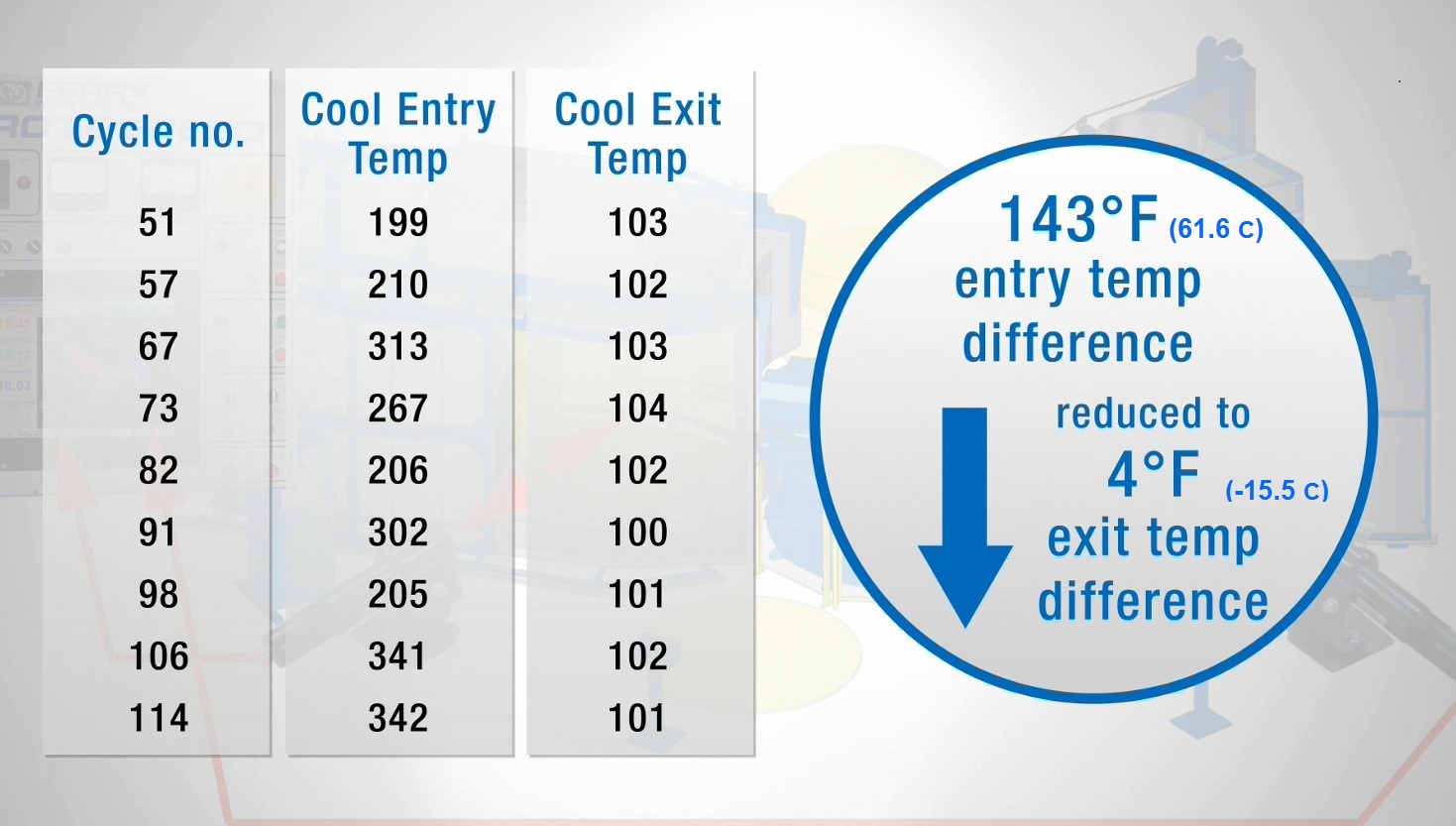
Benefits of Ferry’s IRT:
Automatic recovery from operator induced delays or errors in shot weight.
Compensates for changes in ambient temperature or mold changes.
Consistent part dimensions and properties – quality pars, less scrap or marginal parts.
Optimizes machine, material properties, and energy usage = Higher Profits.
InfraRed Thermometry™ (IRT) for rotational molding machines is available exclusively from Ferry Industries, Inc.
IRT is the first self-adjusting control system for rotational molding machines. By continuously monitoring the surface temperature of the mold, IRT can sense anomalies in the molding cycles that can cause scrap parts and automatically adjust oven or cool times to assure optimum product – removing your dependence on the operator. For the first time, a rotational molding machine that is controlled by temperature, not time.
Consistency is an important key to rotational molding. Without consistency, scrap and borderline product dramatically decrease profits. One of the major causes of scrap and borderline product in rotational molding is change in the ambient condition around the machine. Compensating for these changes in the ambient conditions
(mainly temperature fluctuation) is critical. Currently, machine operators are charged with the responsibility to recognize when adjustments to the oven are required to
prevent scrap. The operator normally does not adjust the cooling parameters.
IRT relieves this responsibility from the operator by having the machine automatically adjust the timing in the oven and cooler to assure the required process parameters to produce optimum product each and every cycle.
Changes in ambient conditions, mold changes, delays at the servicing station, oven or cooling malfunctions can require modifications to the programmed cycle. IRT automatically adapts the oven or cooling times to compensate for any of these and assures that the molds exit the oven and cooler at the specified temperature.
Optimum cure cycle, consistent cooling results, reduced part damage due to problems at the service station and high-integrity of part properties every cycle, are all possible with the automatic, adaptive rotational molding machine control – InfraRed Thermometry™ from Ferry Industries.
Settings for IRT are in the Oven and Cooler station set-up screens.
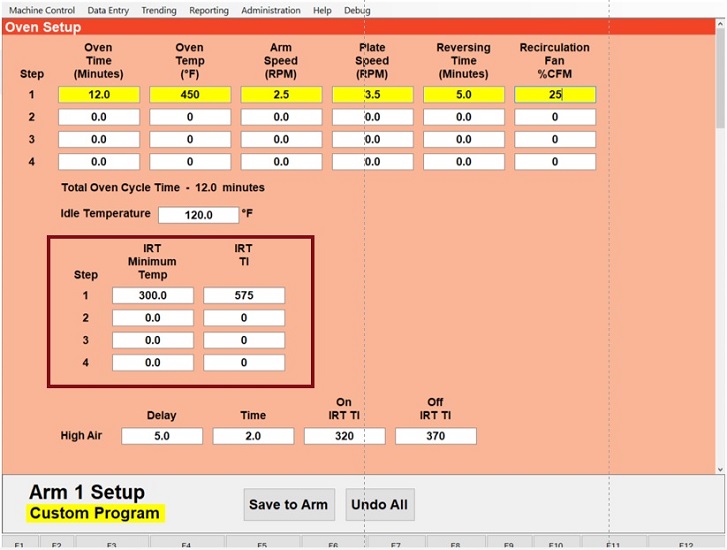
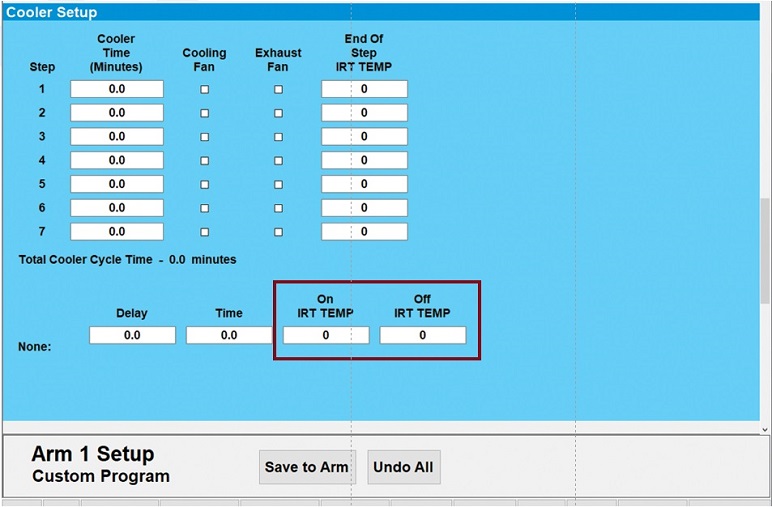
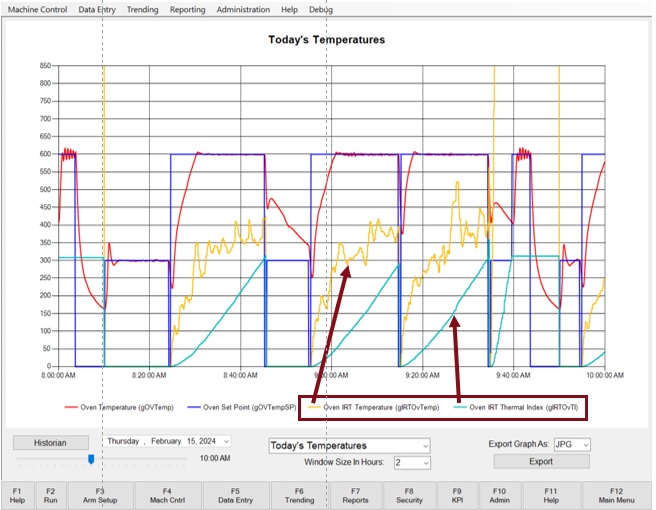
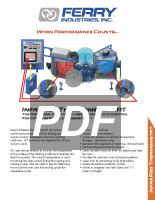